View previous topic :: View next topic |
Author |
Message |
wilsteadt
Joined: 15 May 2010 Posts: 27
|
Posted: Wed Sep 29, 2010 4:49 pm Post subject: Double Hull Plating |
|
|
I was wondering if anyone ever double plated their hull. I have a boat with poor bracing along the keel due to a belly tank that keeps causing the keel weld to crack. My original idea was to grind the weld down and add extra material. Then I started thinking that if I could add an extra sheet of material to the bottom I would solve rigidity issue and be less concerned about hitting rocks. The only negative I have come up with is the added weight and what if water gets in between and freezes in the winter.
Is this ever done or am I and idiot?
Matt.
|
|
Back to top |
|
 |
wilsteadt
Joined: 15 May 2010 Posts: 27
|
Posted: Wed Sep 29, 2010 5:23 pm Post subject: |
|
|
I just realized that this question was my first post and I didn't introduce my self.
My name is Matt and I have a 21' custom boat. I will try to attach a picture. It has a 350 in it now but I am rebuilding a 502 this winter that will go in as soon as possible. I have been reading the posts here for a few months.
I do most of my boating on the Colorado river around Moab, UT.
Matt.[/img]
|
|
Back to top |
|
 |
Kev-o
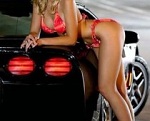
Joined: 17 Jun 2005 Posts: 625 Location: Sylvan Lake
|
Posted: Wed Sep 29, 2010 7:55 pm Post subject: |
|
|
This is done quite a bit on boats built for deeper waters that end up in our neck of the woods. .190" or .250" can be welded as an external keel plate just be sure to blend it in nice around the intake and take it far enough ahead that it is out of the water when on step/plane or you could have a handling issue.
Big improvement on light bottom hulls where it can be a real hassle with belly tanks and what not to do a QT-100 or other bolt on protection.
Kev-o
_________________ Kevin Kipling |
|
Back to top |
|
 |
Boomhower
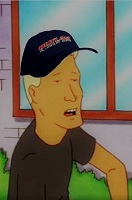
Joined: 03 Nov 2007 Posts: 995
|
Posted: Wed Sep 29, 2010 9:13 pm Post subject: |
|
|
A slab of Qt 100 bolted to the bottom of your hull would be a good upgrade. Welding a slug inside your hull to the keel will strengthen an already weakend hull. But is a pain down the road to fix further issues. What do you have for a bottom now?
|
|
Back to top |
|
 |
wilsteadt
Joined: 15 May 2010 Posts: 27
|
Posted: Wed Sep 29, 2010 10:22 pm Post subject: |
|
|
I am not sure of the thickness of the hull. It is a 12* deadrise I think. I measured the angle at the transom from one side of the keel to the other. I have a dent on one side so it is a little hard to be exact. The difference between 4* is only 2.5 inches at the chine and my math is rusty but I used a angle finder.
The problem is that as the bottom starts to angle up towards the nose the deadrise flattens to about 10* or so and then starts to increase. The stem is flat or truncated and it allows the sweep of the stem to remain relatively flat. ( I hope that makes sense) I will try to post a picture again but I dont have a url to store my pictures and I cant see how to upload them to the forum server.
The result is a relatively flat front area where any chop in the water hits the hull while planing. It gives great lift in rapids and handles great but the ride is rough even if there is not much chop at all. The cracks I have had have happened at this area but I can see other repair welds along the keel in other areas. I dont know if the wrong filler metal was used or what but the weld is the only area that has cracked. I have not taken out the belly tanks yet but I plan to this winter. I can see around some of the tank and can see that there is room for more bracing. I think that I will be adding some bracing no matter what and am thinking about a crosstank to replace the belly tanks but adding thickness to the hull seems that it could only help.
My main concern is water prying the plates apart.
Matt.
|
|
Back to top |
|
 |
bender
Joined: 03 May 2006 Posts: 50
|
Posted: Wed Sep 29, 2010 10:33 pm Post subject: |
|
|
i would go to the qt-100 we have a 18 foot outlaw and put it on last year it is a bit heavier but the added weight really really helped when you are in rougher water for noise and ride ....it was a huge improvment ....and as for what we bought it for the protection it works great...check out my pic in the red deer river launch post we havent even came close to denting that plate
|
|
Back to top |
|
 |
wilsteadt
Joined: 15 May 2010 Posts: 27
|
Posted: Wed Sep 29, 2010 11:18 pm Post subject: |
|
|
I looked up qt 100. It is a high strength steel that I have never heard of. How do you hook it to the boat? Drill and tap? How closely does it need to follow the hull? Is rust a problem? How thick is the material you use? Is it more expensive than aluminum? Do you coat it with anything? It looks really interesting
Matt.
|
|
Back to top |
|
 |
BLOWN INCOME

Joined: 07 Jul 2005 Posts: 127 Location: van down by the river
|
Posted: Thu Sep 30, 2010 8:18 am Post subject: |
|
|
pulled the motor and tank out of my 21 ft eagle and had a piece of 3/8 aluminum bent to match the bottom of my boat.Drilled 1 inch holes in the plate and plug welded it in the bottom between the stringers..before i put this in, my hull would dent really easy,,now its almost indistructable...took a day to do,cost about 300.00 dollors(welded it myself)and boy was it worth every penny.Never had to play with the bottom and it never effected the ride..
Description: |
|
Filesize: |
36.93 KB |
Viewed: |
33074 Time(s) |
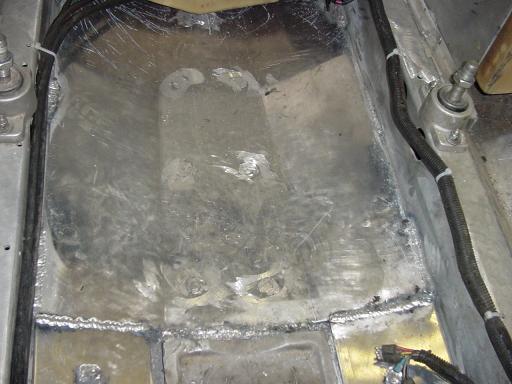
|
Description: |
|
Filesize: |
32.97 KB |
Viewed: |
33074 Time(s) |

|
|
|
Back to top |
|
 |
wilsteadt
Joined: 15 May 2010 Posts: 27
|
Posted: Thu Sep 30, 2010 12:13 pm Post subject: |
|
|
Blown Income, Have you had any problem with water damage in the winter? I know that if I do a good job welding water shouldn't get in but I have noticed that water gets everywhere it shouldn't.
I figure that if I keep it tight the amount of separating due to freezing water will be minimal I just don't know how well I will be able to make the new sheet conform to the hull.
Also, I assume that you sold the distributor to me on ebay. Thanks it is working great.
As far as the steel do you bolt it from the bottom and if you do what bolts do you use? Do the heads get messed up from hitting things?
Matt.
|
|
Back to top |
|
 |
bender
Joined: 03 May 2006 Posts: 50
|
Posted: Thu Sep 30, 2010 12:45 pm Post subject: |
|
|
well i am not the one who installed it so i cant tell you the exact procedure but if you do a search on here for qt100 there is a few pics of what it looks like installed you can vary the size of plate you want to we went with a 2' strip down the middle flairing to 3 feet ( i think ) at the back ...adds about 200 pounds i think it was ...for shallow water boating you do notice this weight as the boat rides a little lower in the water and handles a wee bit different also i think the weight is the biggest factor there ..for lake boating and rough chop its been a blessing we can actually cruise at a fair clip thru chop now ....not like a fiberglass deep v but a huge improvement from what it was ...here is a link to a pic of what it looks like installed from a pic on here http://www.outlaweagle.com/forum/viewtopic.php?t=521&highlight=qt100
also if you look at the builds section there should be a few pics of it being installed also check out the firefish website i think there is a few pics in there under builds to
|
|
Back to top |
|
 |
BLOWN INCOME

Joined: 07 Jul 2005 Posts: 127 Location: van down by the river
|
Posted: Thu Sep 30, 2010 1:22 pm Post subject: |
|
|
did this mod to my hull about 6 yrs ago and everything is good,boats stored outside over the winter with no problems....cheers
|
|
Back to top |
|
 |
rlnah2285

Joined: 20 Mar 2009 Posts: 12
|
Posted: Thu Sep 30, 2010 7:25 pm Post subject: |
|
|
When you install QT 100 steel on the bottom of you boat, you try to fit it up as tight as possible to the keel/ hull itself. Make sure you try to get it to look as straight as possible, sometimes you have to pound the bottom out to get the big dents out or anything that will affect how the boat handles.
Once your happy with the fit, use a good sealant such as sikaflex or duct sealer ( if using duct sealer, be carefull kinda runny sometimes ) to seal it to the bottom of the boat. Leave a good gap around the area around the pump. Weld around the opening for the intake to the steel to sort of blend the area in and keep any water /air from wanting to rush up into the intake and cause it to cavitate. Use a good fastener thats at least grade 8 and countersunk. you want to keep the bottom flat as possible to keep from ripping out bolts and creating leaks lol. Your best to tap each bolt hole and seal it with a good sealant (sikaflex) and use a flat washer to back it all up. Also use nylon lock nuts to keep the bolt from vibrating loose.
Like Kev was saying, you can weld a piece on too. Best way to do that is to add a piece ahead of the qt to just blend it in. like a beaching shoe of sorts.
Hope this helps.
Also too, installing the qt 100 is worth it. Just my two cents as I have learned the hard way !
|
|
Back to top |
|
 |
wilsteadt
Joined: 15 May 2010 Posts: 27
|
Posted: Thu Sep 30, 2010 8:42 pm Post subject: |
|
|
I just read a little about deadrise and realized that I measured wrong. All of my measurements should be cut in half. I have a 6* deadrise with about a 5* up front.
I am thinking about adding some aluminum along the keel and adding steel along either side. What I am really going to do is lay down under the boat in the driveway and try to come up with what would be easiest and best.
Matt.
|
|
Back to top |
|
 |
Kev-o
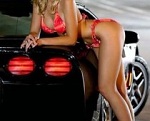
Joined: 17 Jun 2005 Posts: 625 Location: Sylvan Lake
|
Posted: Fri Oct 01, 2010 7:20 am Post subject: |
|
|
There is nothing wrong with QT-100 IMO but do you have the clearance to space the fuel tank up to allow for the bolts and washers
Adding aluminum to the EXTERIOR of the boat is a great fix that is NOT a pain to work on in the future. No holes to leak and no tank to rip up and bolts to undo if there is a problem.
We welded .250" to the exterior of a brand X boat that was damaged and the owner was worried about weight and speed loss (sport jet) and when it was all said and done he picked up a couple MPH.
Could also be done like Blown income did and weld it internally, this requires stripping a good portion of the hull.
Is the bottom pretty bent up right now?
"Just my 2 cents"
Kev-o
_________________ Kevin Kipling |
|
Back to top |
|
 |
wilsteadt
Joined: 15 May 2010 Posts: 27
|
Posted: Fri Oct 01, 2010 12:03 pm Post subject: |
|
|
The bottom is mostly fine except the cracked weld and a dent in the back end that I am going to fix anyway. The dent in the rear happened last time out and I didn't even feel it. It kind of surprised me when I saw it.
Is the 0.25 difficult to form to the hull. It seems that if I had a bunch of holes to weld the sheet to the hull I could work from one end and keep it pretty tight.
I have to admit that having lots of holes in my hull for bolts worries me. I am sure it can be done safely but it also seems like it one more thing to keep up on.
I think that having the steel would make me slide over gravel better but the ease of aluminum would off set that for me.
Matt.
|
|
Back to top |
|
 |
|